Mark Sears is Dunlop’s Product Support Manager. Having worked in the Motorsport department for 20 years, ten of those as Chief Design and Development Engineer for motorcycles, he knows everything there is to know about high performance tyres…
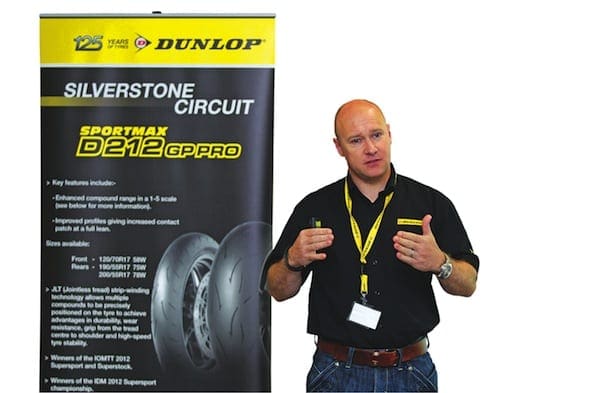
“Every single Moto2 tyre is hand built in the UK by workers at ‘Fort Dunlop’ race department in Birmingham, while the Moto3 tyres are built in Japan. When you consider that 32 Moto2 riders line up on 18 weekends a season and the rules allow them five front and seven rears minimum (up to 11 fronts and 12 rears if it is wet) per meeting, you get some idea of the number of tyres we have to build. And that’s just the Moto2 tyres: a host of other motorsport events need catering for. It’s not surprising the race department runs a 24-hour production schedule…
“The starting point for any tyre is the compound, which most riders will call the rubber. While it does actually contain a small amount of natural rubber, it also has about 20 other components as well as around one litre of oil.
“All the ingredients are fed into a machine called a Banbury, which mixes and then heats them together to produce strips of compound that look like big bits of chewing gum. By altering the mixture we can effect how the compound behaves. More silica makes a better wet weather tyre, more carbon black makes it last longer and more oil can make it stickier – which seems a contradiction, but qualifying tyres contain more oil than race tyres as they’re a softer compound.
“To construct the tyre’s carcass we start with a neoprene sheet, which is effectively an inner tube, and its only job is to stop the air from escaping. The beads are then produced by coating steel in copper, winding them into a circle and then covering in rubber. Rubber doesn’t stick to some steel very well, which is why they are coppered first. The beads are then combined with the neoprene layer on a machine called a former, which helps give the tyre its shape. After a nylon ply layer is added for strength, the tyre’s basic carcass construction is complete and it is moved onto the £2m MRG (Motorcycle Radial Goodyear) machine.
“The MRG winds on strips of Kevlar thread coated in rubber onto the carcass in much the same way you would wind string onto a bobbin in a process we call JLB, or jointless belt. The Kevlar is twisted together before being coated in rubber and by varying the strength of the twist we can affect the carcass’s performance – a tight twist makes the carcass stronger, a less tight one could make it move around more. With this attached to the tyre we cover it with a layer of aramid which uses our N-TEC technology developed through racing and essentially holds the carcass together so that it forms a stronger structure allowing the use of low tyre pressures. All that’s left is the addition of the compound.
“The rubber is extruded through a machine and is wound onto the tyre in a similar fashion as the JLB. We start at one side of the tyre and apply the compound in thin continuous strips until it covers the whole surface. The advantage of this system is that should we wish to alter the compound we can simply introduce a new compound into the extruder, creating tyres with variable compounds across their surface. Once complete, the tyre’s surface looks a bit like a cake that has been piped with icing and isn’t smooth, this is a ‘green tyre’ and is ready for the last process.
“The last stage of tyre production is vulcanization, which is simply the use of heat and pressure to cure the tyre. The ‘green tyre’ is put on a diaphragm that expands to help it hold its shape before a mould clamps over it and it is held in this state for 20 minutes at 10 Bar of pressure and at 200-degrees. The shape and design embedded in the mould determines the tyre’s tread pattern – a smooth mould is a slick, a treaded one is a road tyre. Once removed from the mould the tyre is put on another diaphragm to hold its shape while it cools and then it’s ready to go. Well, once it has passed the testing procedures and been cleaned up – we remove all the ‘hairs’ of rubber, or spue pips to give them their correct name, before sending the tyres out. We want every tyre to look good as well as perform perfectly…”
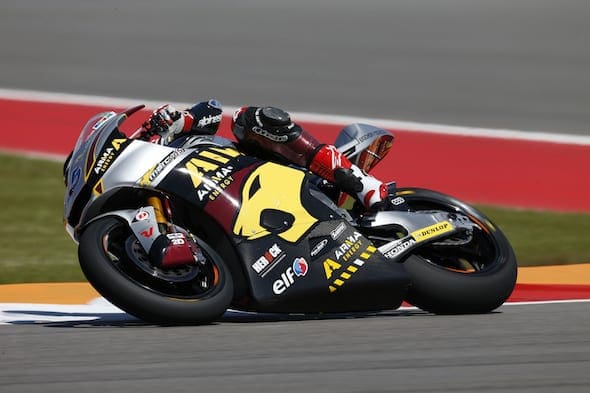